Главный офис
в центре Европы
Гарантия
до 24 мес
до 24 мес
Лучшие
цены
цены
Экономия
от 15 до 55%
от 15 до 55%
Доставка
по России
по России
Все грузы
застрахованы
застрахованы
Бесплатная
доставка
доставка

Alfa Laval P2
Категория - Сепараторы дисковые и центробежные
Официальный сайт Alfa Laval (Швеция) :
www.alfalaval.com
Узнать цену
В нашей компании вы можете выбрать и купить Alfa Laval P2, а также другие запчасти от
компании Alfa Laval с доставкой по всей России, в том числе в ваш город : Дублин. Для запроса цен, сроков поставки
и других характеристик продукции Alfa Laval, пожалуйста, заполните форму обратной связи или пришлите описание необходимых Вам наименований
на электронный адрес info@famaga.ru
Описание
Продукция, изготовленная шведской Alfa Laval компанией, подходит для использования в пищевой, химической, фармацевтической, горнообрабатывающей и нефтяной промышленности.Преимуществом товара является длительный срок службы без необходимости осуществления регулярного обслуживания, а также его первоклассное качество и надежность.Alfa Laval P2 range of decanter centrifuges provides the most cost-effective and high-performance solution for applications in process industries. The P2 decanters are designed for slurries that are often erosive and aggressive. Alfa Laval P2 heavy-duty decanter centrifuges are specially designed to work effectively in corrosive, abrasive and otherwise aggressive operating environments. This makes them ideal for separation duties in industries such as steelmaking and mining, and in the production of pulp and paper, coke, chemicals and petrochemicals, pigments, polymers and fertilizers. Alfa Laval P2 decanter centrifuges establish new benchmarks for separating aggressive industrial sludges and slurries more efficiently than ever before, at the same time as ensuring low power consumption and life cycle costs. Using P2 units makes it possible to:- boost revenue because the process components have greater commercial value
- achieve increased cake dryness and thus reduce the costs of solids disposal
- recover more of the expensive chemical additives used in separation.
Пригласить на тендер
Наш менеджер свяжется с вами в ближайшее время.
Запрос отправлен
Запрос отправлен
Письмо не отправилось
Письмо не отправилось
Оставьте заявку
Мы свяжемся с вами и ответим на любой возникший вопрос.
Запрос отправлен
Запрос отправлен
Письмо не отправилось
Письмо не отправилось
Заказать звонок
Мы ответим на любые вопросы и поможем оформить заказ
Спасибо за вашу заявку!
А пока мы обрабатываем ваш запрос, вы можете найти другие необходимые вам позиции - ведь в нашем каталоге более 10 000 брендов!
Заказывая у нас сразу несколько позиций вы существенно экономите на доставке!
Каталог производителей
Искать
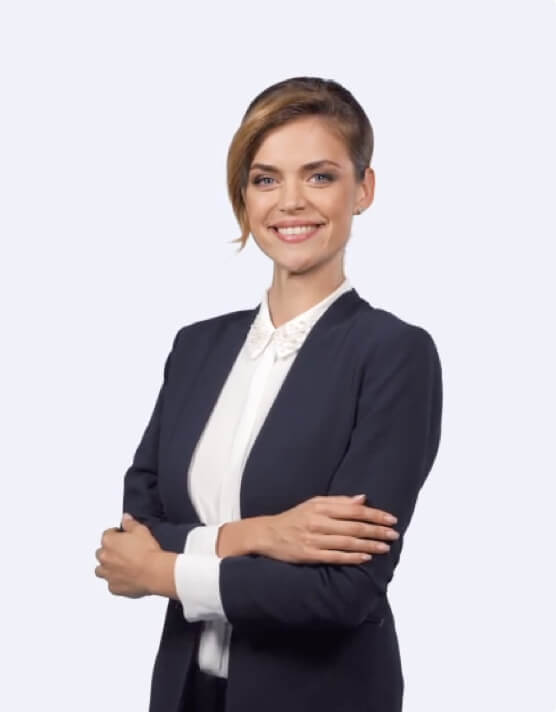
Что-то пошло не так
Кажется, что-то пошло не так. Попробуйте повторить попытку ещё раз позже.
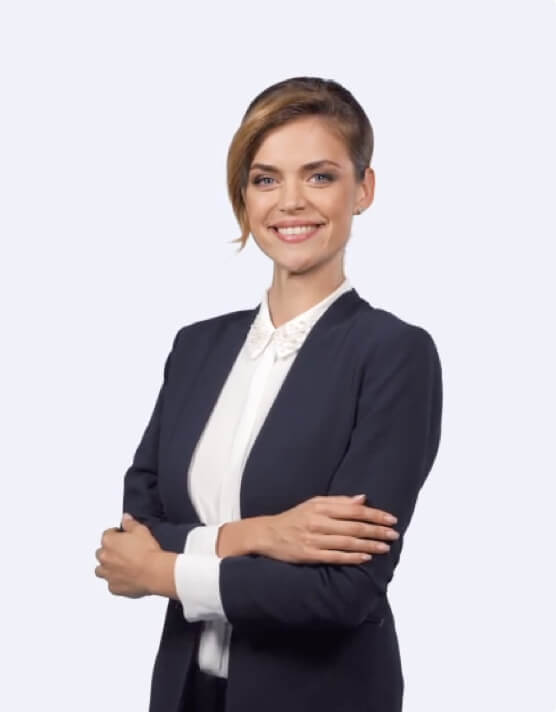